Die Casting
Molten aluminum alloy (zinc and magnesium alloys can also be used) is injected into a metal mold at high speed and low pressure using a die-casting machine. This casting method involves rapid solidification of the metal in the mold at lower temperatures.
Die-casting features include high productivity and automation, excellent dimensional accuracy, minimal post-processing, smooth surface finish of castings, high mechanical strength, and the ability to produce thin-walled, complex, and hollow components.
Materials and Applications of Pressure Casting
Pressure casting is used for a wide range of applications, including:
1. Automotive parts such as wheels, engine blocks, cylinder heads, manifolds, etc.
2. Aerospace components.
3. Electric motor housings.
4. Kitchenware like high-pressure cookers.
5. Electronics industry cabinets.
6. General hardware tools, pump parts, plumbing components.
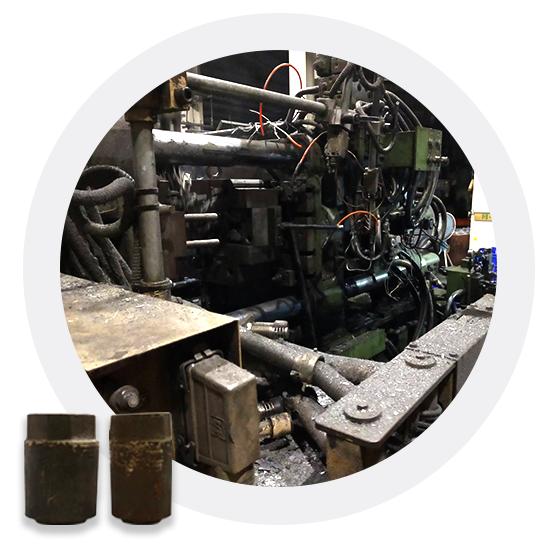
Pressure Casting Process
High-Pressure Casting
In
high-pressure casting, liquid metal is injected into the metal mold at high
speed and pressure. The basic equipment consists of two vertical plates, with
one serving as a fixed plate and the other as a movable one. The mold halves
are placed on these plates, securing the semi-mold. Within these two plates,
one remains fixed, while the other is movable.
This
helps in opening and closing the mold. A specific quantity of molten metal is
poured into an injection cylinder and introduced into the mold cavity. This is
done using a piston driven by hydraulic pressure. After the metal solidifies,
the mold is opened, and the final casting is removed.
The
only difference between high-pressure casting and low-pressure casting is the
method used to introduce the molten metal into the mold.
Hot Chamber Process
The hot chamber process is only suitable for low-melting-point alloys like zinc, which do not corrode or interact with metal canisters and plungers. In this process, molten metal for casting is placed at the required temperature near the machine, sometimes as a part of the machine itself. The injection mechanism is placed inside a heated furnace, with most of it in constant contact with the molten metal. When the injection piston applies pressure, the metal is forced through a gooseneck passage into the mold. During the return stroke, the metal is pulled back into the gooseneck for the next shot.
Cold Chamber Process
In contrast to the hot chamber process, the cold chamber process does not immerse the injection system in molten metal. Instead, the metal is transferred manually or automatically into the injection cylinder via a steel crucible. A plunger operated hydraulically pushes the metal into the mold.
This process significantly reduces the contact time between the injection components and molten metal, prolonging the component's lifespan. However, the high-speed injection associated with cold chamber machines can lead to the entrapment of air in the metal, resulting in porosity in the casting.
Cold chamber machines can achieve injection pressures of over 10,000 psi or 70,000 KPa. Typically, cast steel parts, as well as aluminum and copper-based alloys, are produced using this method.
Low-pressure casting
In a low-pressure casting machine, a crucible containing molten metal is sealed, and pressure greater than atmospheric pressure is applied. The molten metal rises through a riser tube within the crucible and is injected into the upper mold connected to the furnace.
Low-pressure casting characteristics:
High productivity and automation, excellent dimensional accuracy, minimal post-processing, smooth casting surfaces, the potential for further heat treatment to enhance product performance. It is commonly used in automotive components such as cylinder heads, cylinder blocks, brake drums, clutch covers, wheels, intake manifolds, and more.